They are horizontal elements made to prevent vertical displacements in deep excavations and to secure structures against rotation.
MACHINERY AND EQUIPMENT:
Drilling Machine:
- Casagrande C6,C8
- Rod
- Auger
- Drill
- pistol
- Casing pipe
Injection Machine:
- Pump
- Mixer
- Agitator
Stretching Machine:
- power unit
- Jack + Tensioners
- Tension Wedge
- Tension Head
Secondary Machines:
- Water pump
- Generator
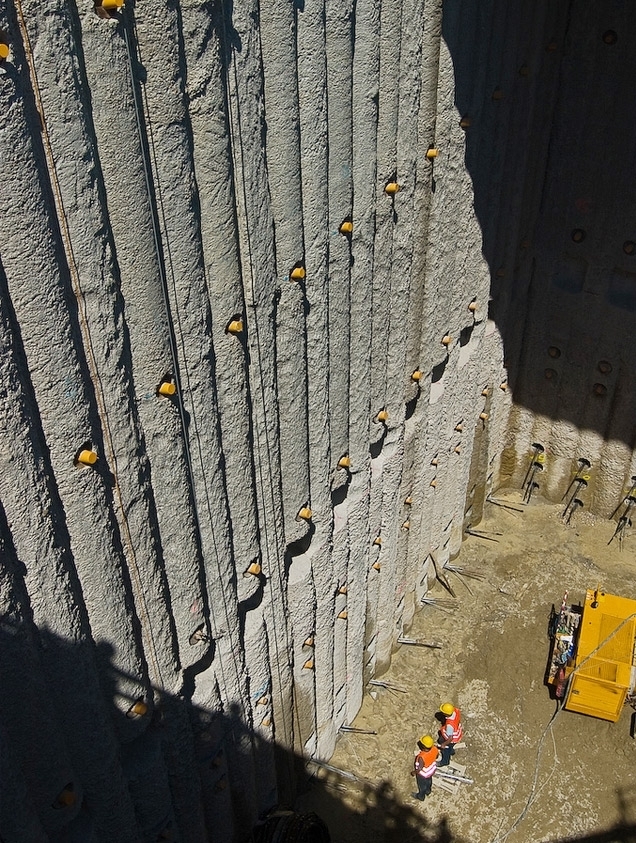
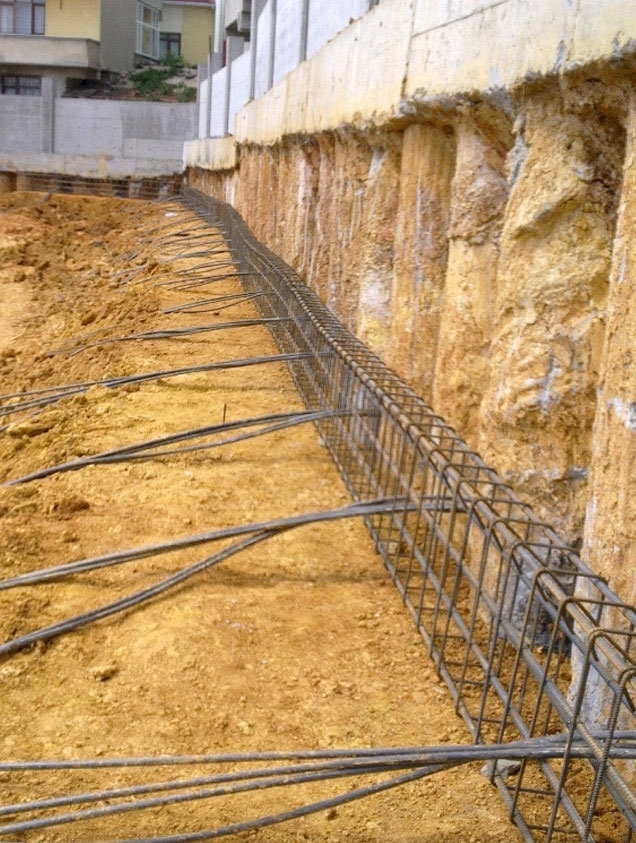
CONSTRUCTION METHODS:
Following the marking of the places specified in the project by the measuring group in the field, the production starts with the anchor material selected in accordance with the structure of the ground.
Drilling Methods:
In anchor drilling, impact, rotary and both methods are used.
Rotary Drilling Method:
It works by transferring the pressure and rotational force given by the machine to the rock drill located at the end of the rods through the rods. Drilling can be done by using the following equipments.
Rock Bits:
It consists of a body and tapered bearings. There are hardened ends on the bearings. The number of these ends depends on the hardness of the ground.
Auger (Auger):
It is used for drilling non-hard plastic clay like floors and throwing them out of materials.
Progression with Casing Pipe:
It is used to prevent debris during drilling on floors containing filling material or underground water. To prevent wearing on the end of the pipe, a carbide made of hard metal is used.
Impact Drilling Method:
This method is used on hard rocks. There are two types of applications. A blow is obtained with a hammer that works, one on the head of the machine (Top Hammer), and the other at the bottom of the hole (Down The Hole).
Headshot (Ball Hammer):
The rotational movement of the machine is transferred to the ground by means of the hammer and rods in the head. The hole diameter can vary between 35 – 133 mm.
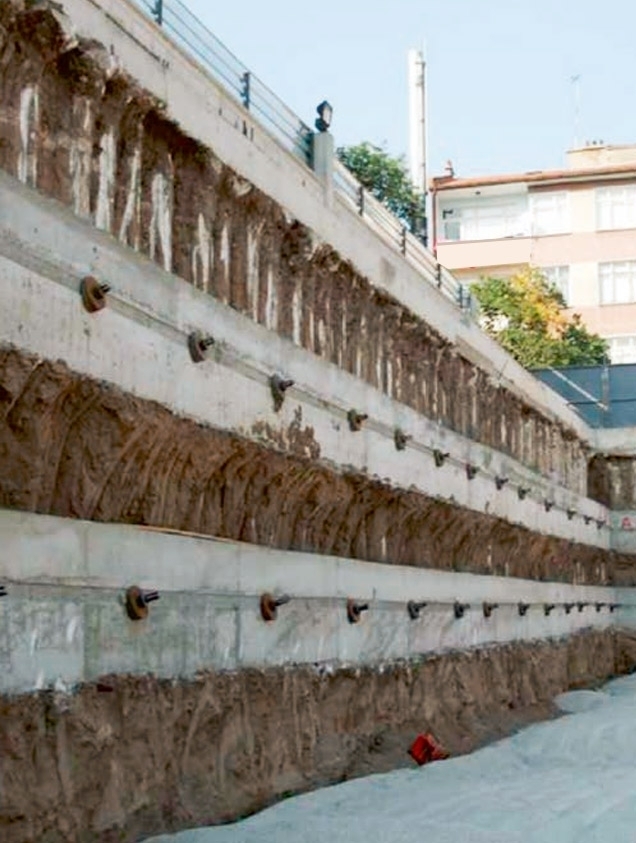
Headshot (Ball Hammer):
The rotational movement of the machine is transferred to the ground by means of the hammer and rods in the head. The hole diameter can vary between 35 – 133 mm.
Hole Bottom (D.T.H):
In this method, the rotational movement of the machine is transferred to the gun at the bottom of the hole by means of rods. While the gun rotates on one hand, it works with the help of the air supplied with the compressor on the other hand and makes the movement of hitting the rock with the raised bit at the tip. The hole diameter can vary between 85-254 mm.
Cleaning Method:
The methods used to eject the material during the hole drilling process affect both the drilling speed and the quality of the hole. Because in order for the hole to progress effectively, it is essential to keep the hole clean by constantly throwing out the cut material accumulated at the bottom of the hole. Air, water or foam is used for this work. Insufficient cleaning during drilling causes bit jamming and rods break off from the joint, leaving the entire tool in the hole.
Prestressed Anchor Harness Preparation:
First, prestressed steel ropes of equal length are cut. These ropes are fixed with spacers and connectors at equal intervals in the root part and the root part is formed. Then the free length of the bundle is insulated with a polyethylene pipe. In addition, 1 or more (specific to the working area) polyethylene pipes are attached to the anchor bundle for injection purposes. The anchor bundle is lowered into the completed hole.
Injection Method:
The adhesion strength between the injection mortar and the tendon depends on the mixing ratio of the materials in the injection, the preparation method and the method of pressing the hole. After the drilling is completed, the anchor bundle is lowered into the hole. Then it is filled from the bottom up with the help of the guide hose. ∼ A second injection is given 1 hour later.
Composition of Cement Mortar:
Portland Cement is generally used in the production of cement mortar. The cement used must be fresh. The potable water used must be of the same quality as the concrete mixing water. Simply put, it should be drinkable. The sulfate rate in the water should not exceed 1% and the chloride should not exceed 5%. There should be no sugar and organic substances in the water. If desired, sand can also be put into the mortar. The sand to be used for the mortar should be fine (grain size less than 2 mm), clean and moisture-free. The ratio can be selected between 1/1 and ½. The most important factor affecting the strength of cement mortar is the ratio of water to cement. The optimal ratio is between 0.40 and 0.45. By adding additional additives into the mortar, it is ensured that the mortar has the desired behavior.
Task of Additive Opt. Dosage (% of Cement Weight)
Extender 0.005 – 0.02
Retarder 0.2 – 0.5
Accelerator 1 – 2
Non-segregation 0.2 – 0.3
Plasticizer 2 –3
Preparation of Cement Mortar:
a) Water of desired quality and appropriate proportion should be poured into the mixer before cement.
b) Then the appropriate amount of additive should be added to the water.
c) Measuring cement.
d) The mixing time is not less than two minutes.
e) Not to be mixed by hand.
Pressure Injection of Cement Mortar:
Pressing the mortar into the hole is done by filling it from the bottom up with electric or air-operated piston pumps. Injection pressure depends on the purpose of the injection, the type and quality of the soil, and the depth of the part to be injected.
Anchor Elements:
- Tendon material
- Load distribution plate
- Anchor head
- Anchor wedges (compressor)
- Separators
- Polyethylene hose.
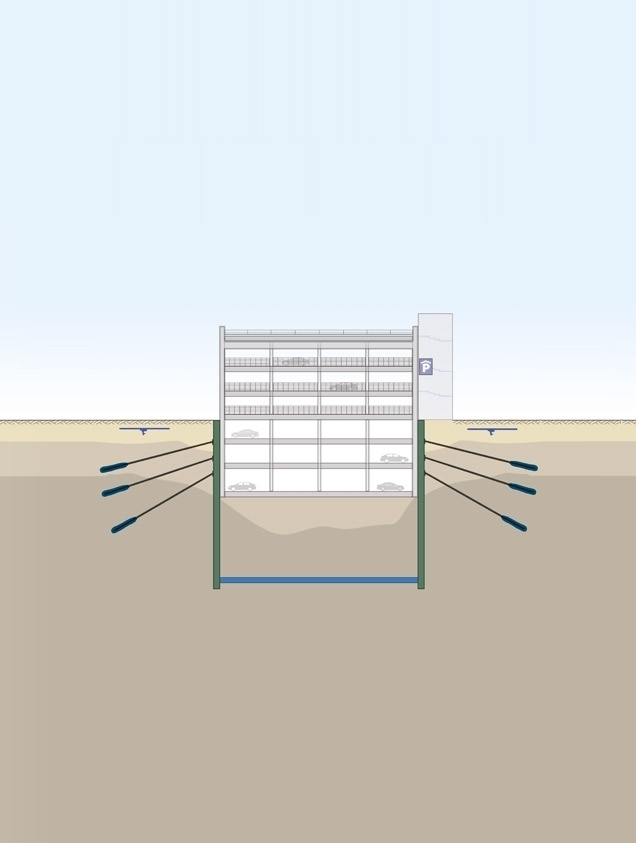
